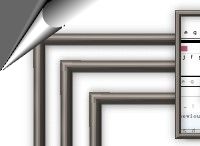 |
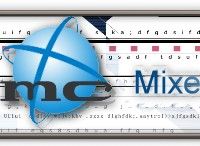 |
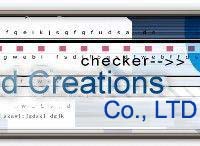 |
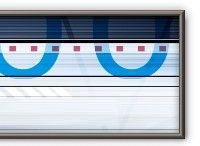 |
|
 |
¡@ |
¡@
QUALITY STANDARD
SAMPLING METHOD
We
use the recognized international quality control standards to conduct
inspections. We refer to the most widely accepted sampling methods.
They are based on mathematical theories of probability and offer the
advantage of clearly defining the number of samples to be drawn for
inspection from a given lot or consignment. They also suggest the maximum
number of defective items allowed in the sample size.
Unless otherwise instructed, Mixed Creations Co., LTD uses the Single Sampling Plan Normal Level II (according to the MIL-STD 105E
standard). This is generally the common requirement for products
manufactured in China.
Acceptable Quality Level (AQL)
As MIL-STD-105E is based on random sampling, therefore
a few defectives are considered acceptable. The AQL is the maximum percent
defective that, for purposes of sampling inspection, can be considered
satisfactory as a process average. Different AQLs may be designated for
different defects such as critical, major and minor defects. The AQLs should
be agreed upon between buyer and supplier before the start of production.
The
following AQLs are usually applied by us unless
otherwise instructed by the client:
Remarks:
Acceptable quality level (AQL) sample inspection methods have been proven to
be accurate over a long run. However, the quality level of merchandise at
destination is generally lower than the per-shipment inspection results.
This may be due to transport, handling, change in environment an/or
reliability problems. Buyers are therefore advised to take this into
consideration when deciding the AQL level.
Defect Classification
The
customer defines the AQL and the maximum number of defective goods allowed
in the sample size.
Defects detected during visual inspection are classified within 3
categories: "Critical", "Major" and "Minor"
¡@
-
Critical: Likely to result in unsafe condition of contravene mandatory
regulation (no critical defect is
accepted)
-
Major: Reduce the performance of the product or is an obvious appearance
defect
-
Minor: Does not reduce the performance of the product, but is a defect
beyond the defined quality standard.
Our Professionals
Our inspectors are graduated in Quality Management from either Hong Kong or
Taiwan universities. With their solid experiences in China business
and local productions in China. We have a lot of experience to evaluate
possible business chance, communicate with the local Chinese to maximize the
mutual profits as a long-term relationship.
How to order an inspection
Normal orders can be made by fax or e-mail at least 1 week in advance. Here are the main steps of the inspection process:
-
Send us by email, fax or phone the contact details of supplier
(phone number, contact name, address) as well as preferred shipment date
if available.
-
We'll send the supplier a booking form to confirm the date and
location of inspection.
-
Once the inspection is finished, a Detailed Report is sent to
you within 24 hours
-
- If the result is satisfying for you, a certificate will be issued to
supplier in order to allow the payment
- If the result is not satisfying, a re-inspection can be ordered after
defective products have been replaced or corrected by the factory. This
will be charged either to the customer or the supplier, depending on
arrangement made.
Back to Service..... |
¡@ |
 |
¡@
¡@
¡@
¡@
¡@
¡@
¡@ |
|
|
Copyright 2007, Mixed
Creations Co., LTD. All rights reserved.
Web site developed by
Monochrome
|
|